Collaborative Robots at the Heart of Cable Manufacturing
Our Windsbach plant is already considered one of the most modern of its kind, but now a cobot is supporting our employees to manufacture more of your cables.
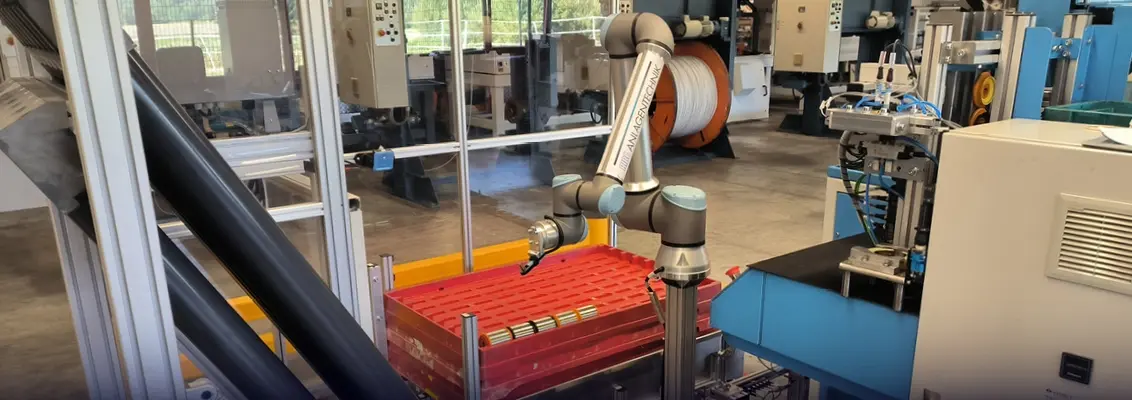
What is Smart Manufacturing?
According to the National Institute of Standards and Technology (NIST), smart manufacturing incorporates changing technologies. Specifically, they define it as: “fully integrated, collaborative manufacturing systems that respond in real-time to meet changing demands and conditions”.
Today, it means warehouses and manufacturing plants use a combination of human and AI-powered systems. For example, adding robotic technology like cobots to the production floor. The benefits include increased efficiency, production, agility, safety, sustainability, quality control, and savings. Making it a smart solution for both the business and you, the end customer.
Types of Warehouse Robots
One robot doesn’t do it all. Every warehouse is different and has certain specifications and automation requirements. Because of this, various robots have entered the smart manufacturing scene, enabling businesses to optimise workflows and production where required.
- Anthropomorphic Robots
- Automated Guided Vehicles (AGVs)
- Automated Guided Carts (AGCs)
- Automated Labelling Robots
- Autonomous Mobile Robots (AMRs)
- Automated Storage and Retrieval Systems (ASRS)
- Case Erectors
- Cleaning Robots
- Collaborative Robots (Cobots)
- Goods-to-Person (GTP) Robots
- Packaging Robots
- Palletising and Depalletizing Robots
- Security Robots
- Sorting Robots
- Unmanned Aerial Vehicles (UAV)
At HELUKABEL, we have various robotic systems in our manufacturing plants and distribution centres. However, our latest addition is a cobot.
What is a Cobot?
For the right definition, we’ll look to the International Federation of Robotics (IFR). A collaborative robot is designed to work alongside humans in various industries and applications.
Cobots have technical features that ensure they don’t cause harm when a worker comes into contact with them. Regardless of whether it’s purposeful or accidental. For example, they feature lightweight materials, rounded contours, padding, sensors, and defined speed and force thresholds.
How Does a Cobot Work?
Most cobots are designed and built using specifications that meet the intended use. Because of this, there are various ways in which the cobot works. At one end of the spectrum, for example, some cobots are designed to be in separate workspaces to the humans while others share the same “cell”.
In cases where the cobot is in a separate workspace, it’s designed so that workers can enter the space without needing to turn the robot off or secure the cell. Simply, the worker can work around the robot and the production line sees no downtime.
For cobots that share the same “cell” as the worker, it is fitted with specialised sensors that detect human motion. Then, when the worker is in the designated workspace, the cobot will work at a reduced speed and force. This allows the worker to operate more efficiently with computer-aided assistance.
When Were Cobots Invented?
The history of cobots stems back to 1995. In this year, the General Motors Foundation offered a research grant to find a way for robots to team with people. Then, in 1996, Northwestern University professors - Colgate and Peshkin - patented the “Cobot”. They defined it as “An apparatus and method for direct physical interaction between a person and a general purpose manipulator controlled by a computer”.
These inventions filled a hole in industries where human performance didn’t meet demand. I.e., they were a smart manufacturing solution to support workers in completing tasks that led to chronic pain or fatigue, ultimately resulting in slowed or halted production. For example, small components handling, repetitive strain, or final assembly tasks.
Using A Cobot in Cable Production
Collaborative robots have a role in various areas of cable production. One of which is with screening material. At HELUKABEL, for example, our cable and wire assembly requires the delivery of screening material on large drums. However, to process the material, it needs to be wound onto smaller spools on the automated braiding machine. Once empty, the spool needs to be placed in the winding machine and removed again when fully wound.
It's monotonous work which, until now, has been done by hand. Much to the pleasure of our employees, a cobot is now performing these tasks automatically. Now, they can focus on other important tasks within the cable production process.
With a cobot in a cable production facility, a magazine of 200 spools serves as a buffer to reduce downtime and boost productivity. In practice, the loaded spools are stacked onto a pallet. From here, our employees can comfortably mount the spools onto automatic braiding machines.
HELUKABEL’s New Cobot
Today, we’re celebrating the introduction of these smart manufacturing solutions. A new cobot has been added to our Windsbach facility in Germany.
Speaking with Peter Bluhm, our Project Lead, he said “Manually handling the spools was not only monotonous but made keeping up with increasing production speeds exceptionally difficult”. "With the new cobot, teams operating the braiding machines not only work more ergonomically but more efficiently. [...] By automating this process step, we can save a lot of time and effort", says Bluhm. "This is right in line with our lean management concept”.
At HELUKABEL, we’ve integrated our cobot with a safety system that means our employees don’t need additional protective equipment. This entire safety system is certified by the TÜV, a group of independent testing organisations.
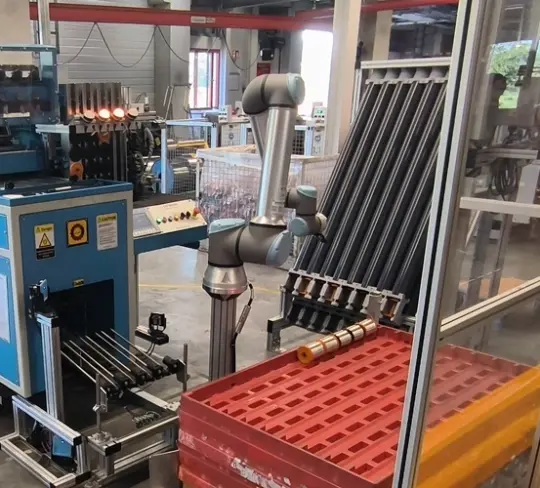
While this is a significant milestone for our production facilities, we’re still innovating. As we aim to maintain our status as having one of the most modern plants of its kind, we’ll continue to innovate with smart manufacturing practices. Whether it means integrating robots or redirecting heat emissions for sustainable heating . Our Windsbach production site has even more automation and digitalisation coming its way. Follow our stories to stay up to date.