Preventing Copper Conductor Oxidisation: A Guide
This is your guide to understanding what copper oxidisation is, why it occurs, what the issues are, and how to prevent it with your copper conductor cables.
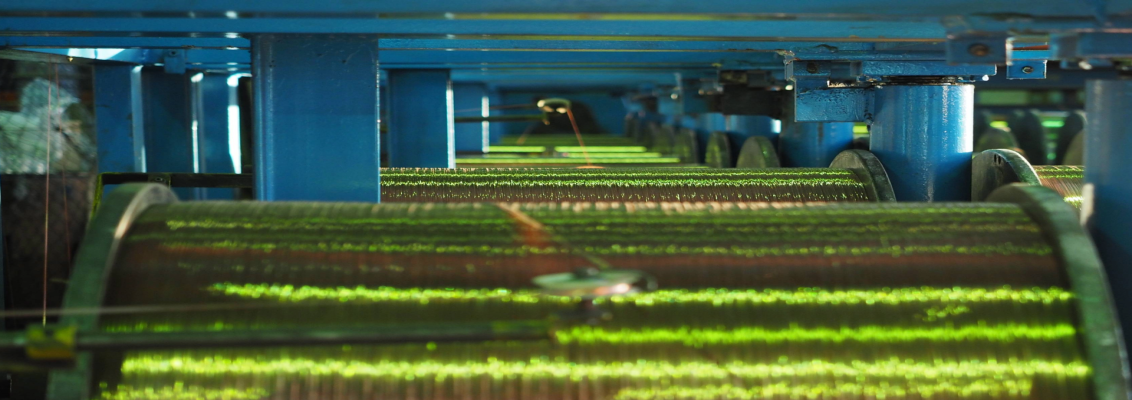
A common concern we hear down the grapevine is about the risk of copper conductor oxidisation. This generally happens when the cable hasn’t been used for an extended period. However, it may also occur due to environmental and application factors. That’s why we’re deep-diving into the best practices of using cables with copper wire conductors.
This applies to various industries and applications. From manufacturing plants and line-building to agriculture and port reeling. Significant quantities of cable are used to ensure the effective transmission of power and data. However, there may be times when the cable is not fully utilised, making oxidisation risk mitigation even more important.
Why Copper Conductor Oxidisation is a Risk
Copper is used within many electrical cables because of the various properties it holds. This includes its general corrosion resistance. But that doesn’t mean copper conductor oxidisation won’t happen with the right conditions.
When copper does oxidise, it can affect its electrical conductivity and safety. Essentially, when the surface changes with oxidisation, it begins to resist conductivity. In industry and infrastructure applications, this could mean decreased efficiency and compromised quality.
How to Identify Oxidised Copper
Identifying oxidisation can easily be done just by looking at the copper conductor, itself. The copper colour fades after being exposed to certain elements. The copper may also appear to have a black layer forming on top of it. This is a result of additional materials being used in the cable’s insulation such as Lead (Pb) and Sulphur (S).
It’s worth noting that copper oxidisation and corrosion don’t only occur when the copper is exposed to the air. It may also happen when the cable is exposed to Chlorine (Cl) or the Hydroxyl Group (-OH). In this case, the insulation becomes slightly acidic, making the copper conductor more prone to oxidisation.
How Manufacturing Affects Copper Oxidisation
During the cable manufacturing process, the cable’s quality can be determined by the input copper. If the quality isn’t guaranteed and impurities are present, corrosion can be a risk down the line.
In addition, the copper wire drawing process needs appropriate drawing technology. This is to ensure the copper conductor doesn’t come into contact with oxidising machine oils. Similarly, during the cooling stage, correct process control should minimise moisture penetration and avoid later oxidisation.
Before shipping, the manufacturing process relies on the safe and effective storage of the cable. If the cable hasn’t been correctly sealed and stored, the copper conductor has prolonged exposure to oxidising elements.
How to Minimise Copper Conductor Oxidisation
There are a few ways to mitigate the risk of copper conductor oxidisation. This can occur at source by the manufacturer, during distribution from the supplier, and with you.
It’s vital to conduct due diligence by researching the company you source your cable from. Reputable manufacturers will adhere to strict production processes and ensure the copper is of a high standard.
With standard lengths of cable, manufacturers typically use cable ends. However, when the cable is cut to specification, it’s not always possible. So, you’ll receive cables on drums wrapped in an outer plastic film. In these cases, reputable manufacturers will cut the oxidised cable ends before it’s delivered to you.
Once you have your cable, you should use electrical tape and caps to preserve the remaining cuts for long-term storage. Various caps ranging from 25mm to 120mm with thicknesses from 1mm to 3mm are on the market. Choose a high-quality cap that fits your cable’s specific dimensions to optimise storage and limit air exposure.
- Buy from reputable manufacturers
- Ensure cable ends are always used
- Use electrical tape for long-term storage
- Have expert cable matching for your application
How are Cables Stored With HELUKABEL UK?
At the UK warehouse, we take cable quality and performance seriously. We use a temperature-controlled environment where cable drums are organised onto well-ventilated pallets. When cables arrive from our manufacturing sites, our team performs rigorous checks on the cable caps and outer plastic film.
In short, copper conductor oxidisation is unavoidable to an extent. By adopting best practices and prevention methods, you can reduce the chance of cable damage and the need for replacements.
To know more about the quality of HELUKABEL copper conductors call our team today on 0151 345 0808.