It's our mission to lead in the production of high-performance cables and wires. We do this by running rigorous tests using dedicated facilities and equipment.
OPTIMAL CABLE SOLUTIONS
The challenges faced by modern cables and wires are multifaceted; moving applications exceeding ten million cycles, severe mechanical and chemical loads, tricky bending radii, and space-saving hybrid solutions.
To ensure a faultless operation, all new products undergo testing at our R&D centre in Windsbach, Germany. Here, we bend, pull, grind, and ignite the cable for all it’s worth using state-of-the-art ageing ovens and more.
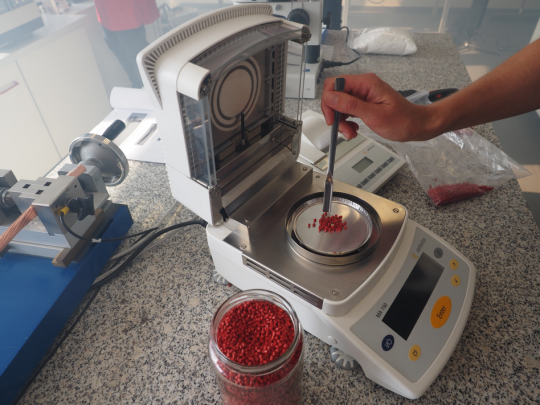
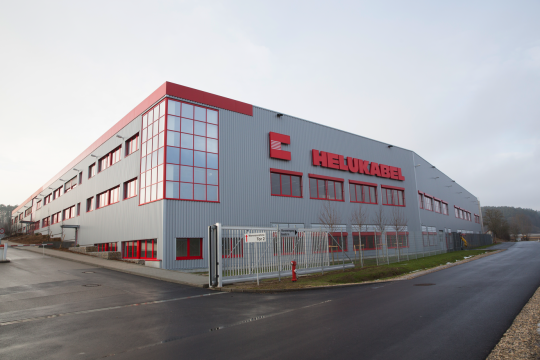
OUR TESTING FACILITIES
Every test we perform is in accordance with national and international standards, guaranteeing your cable's quality.
- Drag chain testing equipment
- Wind power cable testing in Testing Towers
- Fire testing equipment
- Abrasion testing equipment
- Bending and torsion testing facilities
- Aging furnaces according to UL, VDE, CSA, HAR, TÜV, and CCC
BEND RADII TESTING
We test the banding capacity of our cables and wires to ensure they meet the mechanical strength needs of your application. Frequent directional changes may lead to your cables breaking; so we use specialised equipment for testing with both two and three reels. We simulate various loads and bending radii to evaluate what our products can reliably withstand in everyday use.
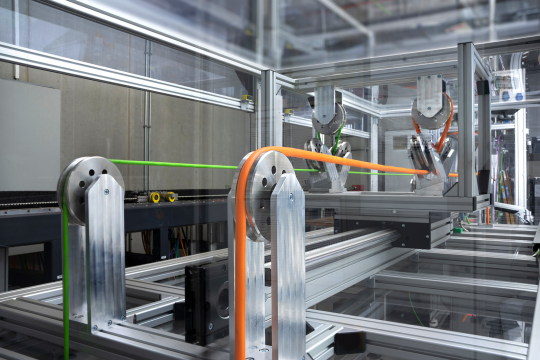
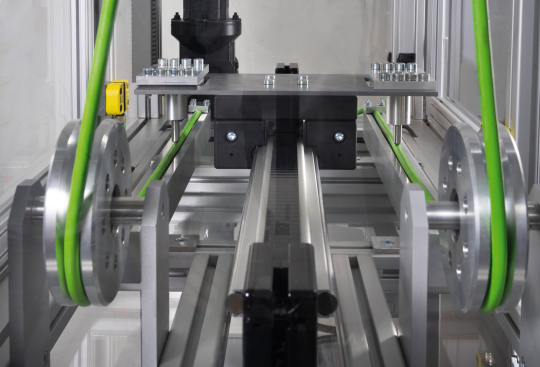
ABRASION TESTING
We test the banding capacity of our cables and wires to ensure they meet the mechanical strength needs of your application. Frequent directional changes may lead to your cables breaking; so we use specialised equipment for testing with both two and three reels. We simulate various loads and bending radii to evaluate what our products can reliably withstand in everyday use.
KINK TESTING
In addition to bending radii tests, we ensure our cables function optimally without the risk of a kink. As bending loads are part of the lifecycle for cables and wires in moving applications, they ultimately lead to damage. Because of this, our laboratories run specialised testing against sheathing and conductor materials to avoid unexpected expensive malfunctions, machine failures, or fire hazards.
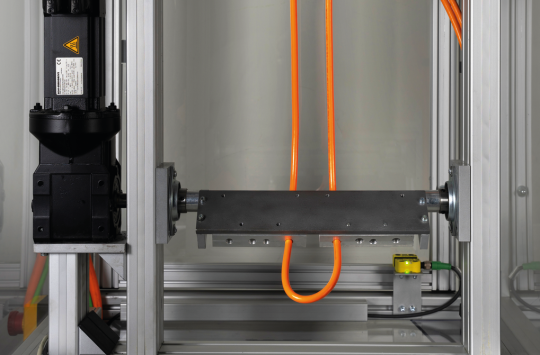
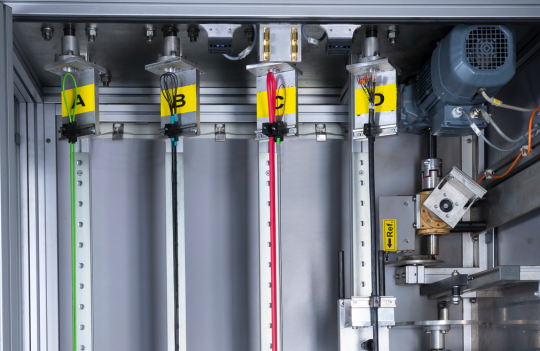
TORSION TESTING
Using both Audi and Käppner Torsion Test Equipment, we simulate extreme torsional loads. We do this against a cable's own axis to evaluate the lifespan and reliability of the materials used. This is especially important for multi-axial applications such as industrial robots and other moving machines where the cable is subject to daily torsion.
DRAG CHAIN TESTING
After acquiring EKD Systems, we've brought drag chain testing in-house to maximise quality assurance testing in our dedicated facility. We test drag chains for all moving applications of short, medium, and long distances at slow and fast speeds; testing against different travel distances and chain radii enables us to simulate various operating conditions.
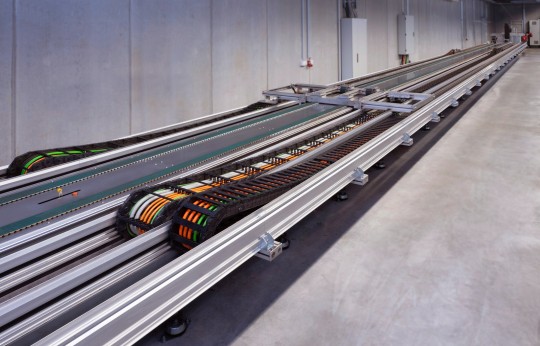
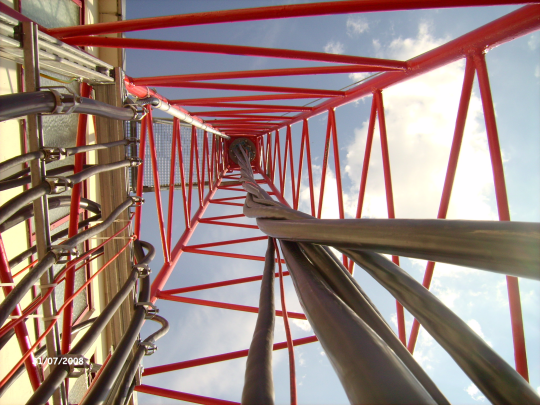
WIND POWER TEST TOWERS
Applications such as wind turbines expose cables to strong torsional forces. Therefore, your cables may experience electrical and mechanical deterioration. That's why we check cable torsion resistance in purpose-built test towers with a maximum speed of 0.8 U/min and a ±150° twist per metre loop. The results enable you to access high-quality power cables that prevent expensive failures.
FIRE TESTING
At our testing facility in Windsbach, we use ultra-modern testing equipment to exceed conditions encountered in practice. This goes for fire testing, too. Testing in accordance to DIN VDE regulation, we test for the behaviour in fire, the corrosivity of combustion gases, the continuation of insulation, the non-halogen verification, the smoke density, and the continued functionality.
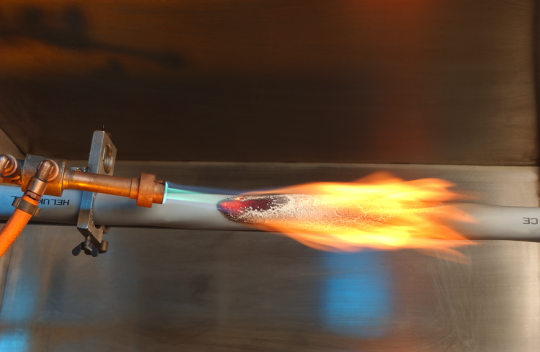
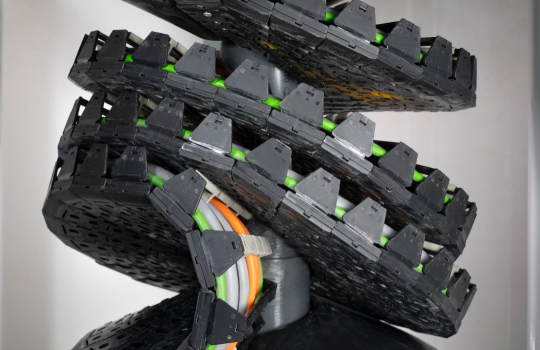
TWISTER TESTING
Some applications subject cables to torsional and bending movements at the same time. Because of this, we look to our "Twister Test" to simulate loads applied in highly dynamic applications with a special drag chain. For each cable we test, the travel distance and maximum angle of rotation are determined by the drag chain but can reach a maximum acceleration of 5000°/s².
INTERNATIONAL APPROVALS
At HELUKABEL, our products meet the following standards, regulations, and approvals across the globe (A-Z):
Austria | Österreichischer Verband für Elektrotechnik (Zeichenvergabestelle) | |
Belgium | Comité Electrotechnique Belge (CEBEC) | |
Canada | Canadian Standards Association (CSA) | |
China | China Compulsory Certification (CCC) | |
Denmark | Danmarks Elektriske Materialkontroll (DEMKO) | |
Europe | Communauté Européenne (CE) | |
Finland | FIMKO LTD | |
France | Union Technique de I'Electricité | |
Germany | VDE-Prüfstelle (Verband Deutscher Elektrtotechniker e.V.), & Fraunhofer Institut, Produktionstechnik und Automatisierung | |
Italy | IMQ Instituto Italiano de Marchio Qualitá | |
Netherlands | Naamloze Vennootschap tot Keuring van Electrotechnische Materialen (KEMA) | |
Norway | Norges Elektriske Materiellkontroll (NEMKO) | |
Russia | GOST-R Zertifizierung (SGS) | |
Sweden | Svenska Elektriska Materielkontrollanstalten (SEMKO) | |
Switzerland | Schweizerischer Elektronischer Verein (SEV) | |
United Kingdom | BSI British Standards Institution (Licensing Office) | |
United States | Underwriters Laboratories Inc. (UL) |