The Aufmaster: Your Best Friend for Inventory Management
For many businesses, the year’s end means inventory time. This is true for us, too. But what does it mean, what does it entail, and how can it be made easier?
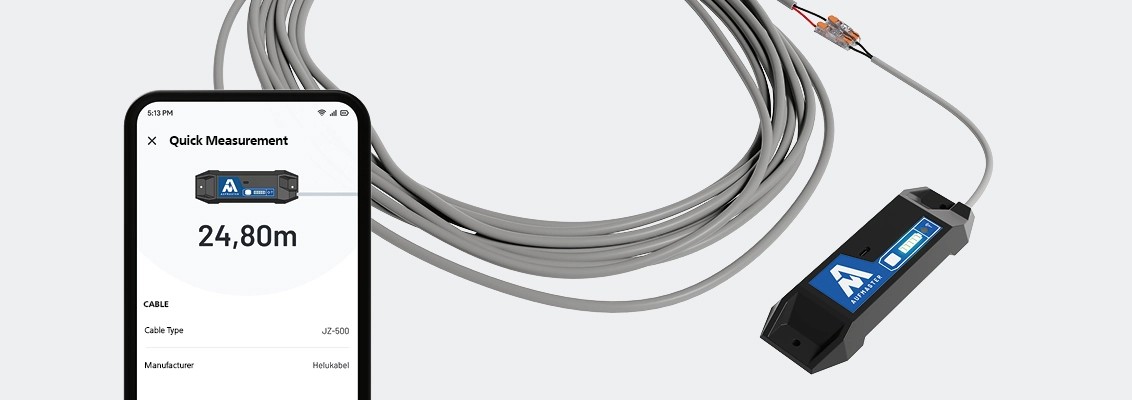
We know inventory management can be cumbersome and time-consuming, especially for large-scale warehouses. Cables and wires are no exception. But when they’re stored on drums or in rings, and have various lengths that aren’t easily measurable, it makes it all the more difficult. Unless, of course, you have the right tools in your back pocket…
Are Inventory and Stock the Same Thing?
Yes and no. All stock is inventory but not all inventory is stock. That’s because stock refers to all components of the business available for sale. Inventory, on the other hand, is everything within the business classed as an asset. For example, unfinished products, computers, warehousing equipment, etc.
When Should an Inventory be Done?
Inventories can occur on a monthly, quarterly or yearly basis. As long as they’re done at least once per year in line with the accountancy period, it’s golden. It’s used to understand the company’s value, bottom line, loss, and ability to continue. This information is used for accounting as the ending inventory is noted on the balance sheet.
What is the Inventory Turnover Ratio
The inventory turnover ratio gives you an idea of how many times you turned over your inventory over a given period. It’s a useful metric to have because it can help make better business decisions for efficiency. Even day-to-day. E.g., dividing the value by the number of days in the period gives the average number of days it takes to sell your inventory.
How Inventory is Calculated
Inventory is calculated through a few means, First, the beginning inventory balance needs to be determined. Then, the cost of goods sold (COGS) can be subtracted from that value. Finally, the purchases of new materials should be added. Stock like cables and wires can be checked using specialised inventory management tools.
Which Inventory Method is Best?
Generally speaking, there are three common inventory methods. The one you use will depend on the industry you’re in and how you want to present your accounts.
- LIFO: Last in, first out. When you want to present lower profits, using the LIFO method is for you. When considering inflation, your most recent inventory additions will be your most expensive. As a result, if you sell this stock first, it would record lower profits. The benefit of this is lower tax liability.
- FIFO: First in, first out. This is best for industries that use or produce perishables. E.g., the food and beverage industry. Essentially, the oldest stock is sold first. This can increase your net income but would give you a higher tax liability. That said, this method is ultimately a popular choice across the UK.
- WAC: Weighted Average Cost. The average cost of all goods, regardless of age is used. It’s a good balance for inventory that is very similar but changes in model or colour. However, this can lead to goods being sold at a loss if the costs increase. Because of this, it’s not well-used in the industrial and manufacturing sectors.
How an Inventory System Works
An inventory management system is the way you choose to track your inventory. Whether via a simple spreadsheet or using a dedicated piece of software. An effective inventory management system offers greater visibility, helps you meet customer demand, gives you a better understanding of profits, and accurately reports on finances.
The Aufmaster Inventory Management Tool
The best inventory management system is the Aufmaster . When calculating your cable and wire inventory, this tool accurately measures cable length and records it in its dedicated cloud-based software.
The idea behind the system is the stuff of genius. It provides industrial, commercial, and craft businesses with an efficient solution for the inventory-taking of cables and wires.
The Aufmaster tool is connected to the end of a cable or wire with two clamps. It doesn’t matter if the cable is wound or not. Then, the device measures the cable’s length using a patented measuring technique. The data is then automatically stored within the dedicated Aufmaster App. This way, you can view and save all measurements on your mobile device without having to wind any cables.
The app transfers data in real-time via the Internet to your company accounts with Aufmaster. The cloud-based software controls and organises your projects, inventories, and measuring tools on various cable drums. So, with less work, you have more time to focus on other tasks.
The Aufmaster is designed to measure cables from 0.25 mm² and can detect lengths between 10 and 1,500 metres. The app, on the other hand, can be used beyond cables and wires. The entire system is designed to be the single solution for all your high-volume items and consumables. It’s an efficient, uniform, and innovative system for taking the stress out of inventory season.