Kink and Abrasion Cable Testing
Most cables are subject to various mechanical stresses. So, we use specialised testing such as kink and abrasion checks to verify the quality of our cables.
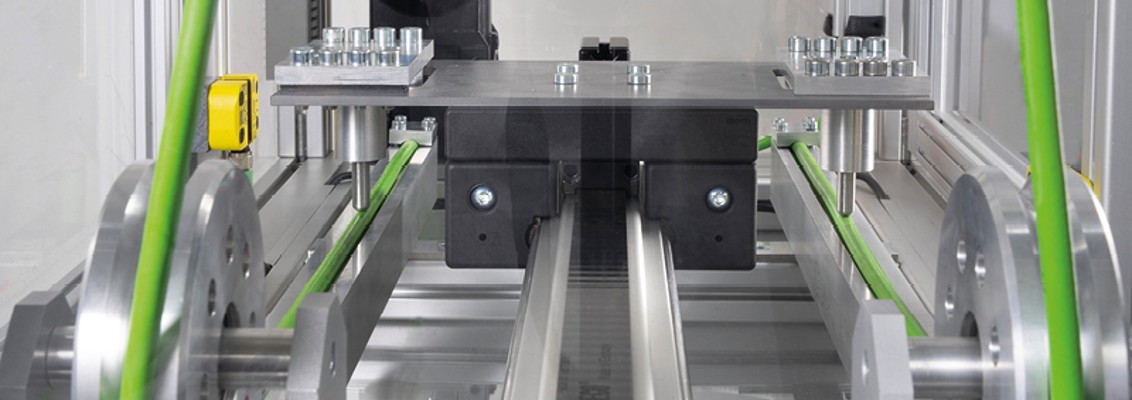
What is Cable Breakage?
There are various ways a cable can become damaged. All of which are dangerous and mean the cable needs to be replaced. For example, a core rupture, a corkscrew, insulation damage, jacket damage, and shield wire breakage.
One of the more common forms is when the cores of the cable break apart because of abrasion or kinking. At this point, the electrical connection at that location is completely disrupted. This risks the electrical current overloading in the remaining cable areas. The cable will then have increased current densities, overheat, and have damaged insulation, resulting in short circuits. With short circuits or electrical arcing, there’s a big risk of a cable fire. And, statistically, it’s one of the most common causes of fire.
Why Cable Testing is Important
Kinks or abrasion damage is caused by the environment and mechanical load of the application. More often than not, this kind of damage is a result of the cable coming into contact with other machine components.
Constant friction leads to long-term damage to the cable’s sheath and core insulation. Alternatively, the bending load is a part of everyday life for cables and wires in many dynamic applications. However, when a cable is used out of specification or with unmatched components, it leads to the same level of damage.
Cable testing in a controlled environment allows cable manufacturers like us to determine the best use for each cable. It also identifies which materials, sheathing, and cores are best for various applications.
How Does Product Testing Work?
Product testing is different for every cable and accessory on the market. Some cables, for example, need additional type tests and others need more rigorous testing. It all depends on the end use.
The challenges faced by modern cables and wires are multifaceted. E.g., moving applications exceeding ten million cycles, severe mechanical and chemical loads, tricky bending radii, and space-saving hybrid solutions.
For electrical cables, specialised cable testing equipment determines product properties. For example, the bending radius of a cable, its ability to withstand abrasion, its fire resistance, how well it’ll work with drag chain, and more. It does this by subjecting a section of cable to a series of harsh environments and assessing what happens.
Abrasion Testing
Cable abrasion occurs when a cable consistently comes into contact with another component. This results in friction, heat, and wear. But there are many applications such as line building or port operations where this contact is unavoidable.
So, to determine a cable’s resistance to abrasion in these environments, a certain test is carried out. We evaluate the suitability of sheathing and insulation using a metal pin. That metal pin is rubbed back and forth against a fixed cable resulting in friction. At HELUKABEL, our cable testing equipment can reach speeds of 400mm/s and acceleration of 2000mm/s2.
This test lets us accurately simulate highly dynamic applications. The results also allow us to determine what effects friction has on the function and longevity of each cable.
Kink Testing
Cable kinks occur when a cable is bent beyond its design. This is more common with class 1, class 2, and class 5 cables as they’re less flexible than class 6.
Specialised kink tests determine a cable’s resilience to torsion and tension. When a cable ultimately gains a kink, it affects its impedance and means the cable must be replaced. Using cable testing equipment at HELUKABEL, we insert a section of cable into a moving device before adding a kink in a predefined location. Throughout the test, our equipment can reach speeds of up to 440°/s, accelerations of 2,000°/s2, and a maximum torsion angle of 180°.
An engineer will only pass a cable if it can withstand these extreme mechanical loads without sustaining damage. However, when we have the results, we can accurately plot the suitability and lifespan of a cable in an ideal application.
Read more about research and discovery at our Windsbach facility
Product Testing and Certification at HELUKABEL
At HELUKABEL, we research, innovate, design, and develop electrical cables to a high standard. But we’ll always check the end product meets the original specification. To do this, we use leading cable testing equipment such as dedicated wind power test towers and fire facilities.
Ensuring a faultless operation, we test all new products at our research and development centre in Windsbach, Germany. This enables us to produce and distribute cables with quality materials that minimise impact and accurate specification sheets that minimise downtime.
When you read a HELUKABEL specification sheet, you know that that cable has been manufactured and tested according to international standards including DIN VDE. If you have any questions about our cables or specification sheets, contact the team by clicking here .
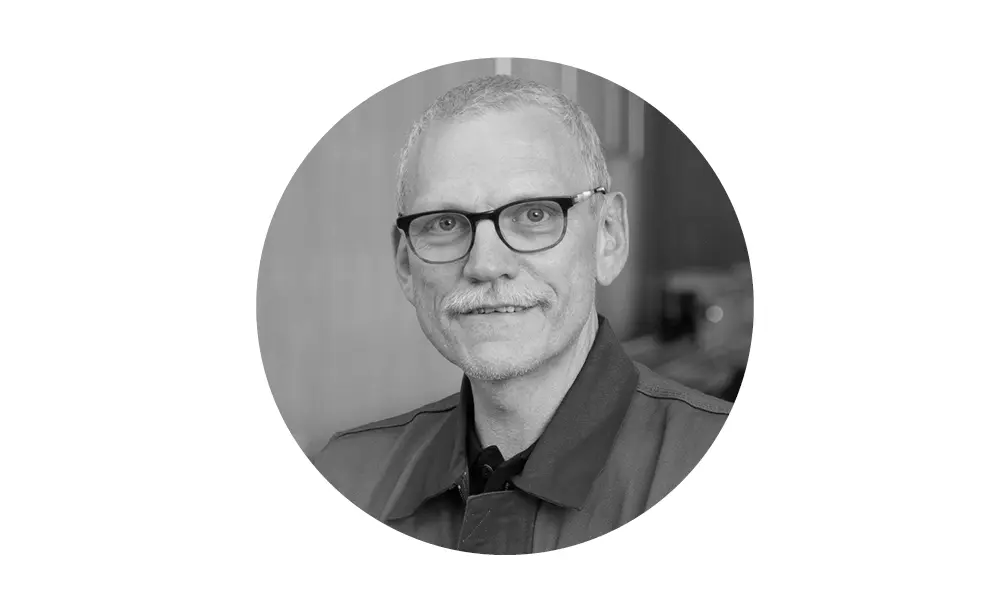
How Can I Best Protect Against Cable Breakage?
We asked our expert, Günter Meyer, the Head of Dynamic Testing in our Winsbach facility, about the best ways to protect against cable breakage. Here’s what he said:
“There is a number of ways. The best way would be to avoid potential contact points [...] however, it’s not always possible. [So] the choice of appropriate sheath material is important. Cables made of polyurethane (PUR) have the highest resistance to friction. Even other thermoplastic elastomers (TPE) exhibit a high abrasion resistance. Polyvinylchloride (PVC), however, is not as resistant. It is also possible to use additional sheathing, such as heat-shrink tubing, braided sleeving, or fabric tape. Alternatively, drag chain can help protect the cable and avoid abrasion.